
10 Apr 2024
For many New Zealanders, 2023 was a year when the weather gods turned toxic, unleashing floods and pummelling critical infrastructure. That made it a demanding year for engineers, called on in the aftermath of disaster to find a solution to the impassable bridge or broken highway. But engineering emergency fixes is a perennial requirement of the job and, often, the clock is ticking. Loudly.
The Auckland sinkhole
It’s December 2023, and Sharon Danks CMEngNZ CPEng IntPE(NZ) is watching the rain through her window. No surprise there: Auckland experienced unprecedented rainfall in 2023, starting with a January rainstorm that broke all records, followed by Cyclone Gabrielle.
Head of Service Delivery for Watercare, Sharon says among other effects, the incessant precipitation triggered at least 30 sinkholes across the region, most of which went unreported to the public. But then came Monday 25 September, when a massive sinkhole opened in Parnell. Within 24 hours, it had grown into a 12-metre-by-12-metre tomo, like a portal to the underworld suddenly appearing on the fringe of the city’s CBD. In fact, it was worse than that: 13m below, the historic brick-lined Ōrākei main sewer, part of a combined wastewater and stormwater network serving central and west Auckland, had been blocked by debris. Sewage was soon overflowing into parts of the Waitematā Harbour, closing beaches.
We had to get everything done in such a public way as well, in the middle of Parnell, with lots of media interest and pressure to minimise noise and disruption and keep traffic flowing and businesses open.
Faced with an environmental emergency, Watercare responded at pace. The immediate priority was to secure the sinkhole to prevent more debris raining onto the 2.1-metre-diameter pipe, and to redirect overflows to points in the harbour where stronger currents could help disperse the wastewater. Meanwhile, Watercare’s engineers were designing a temporary fix until the Ōrākei sewer could be repaired. The bypass they devised involved building New Zealand’s largest temporary pump station, with capacity to pump 600-litres-per-second, and laying 450-odd metres of 600mm polyethylene pipe overland along St Georges Bay Rd and through a reserve.
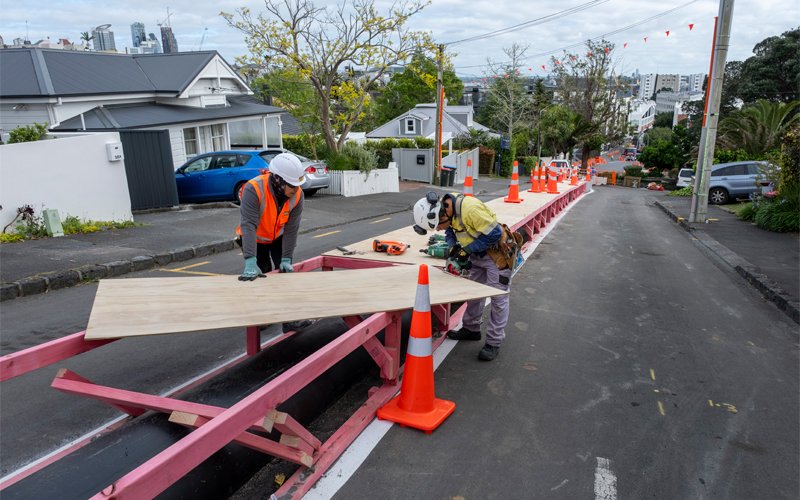
Plywood enclosures prevented the temporary pipe from expanding in the heat. Photo: Watercare
Sharon says several aspects had to be carefully worked through. These included ensuring there was enough head to pump from and designing the hydraulics. Also, finding ways to prevent the polyethylene pipe from expanding in heat – they built plywood enclosures at critical points and used cooling fans. Plus, designing the connection where the temporary bypass discharges back into the Ōrākei sewer “so that it didn’t blow a small manhole out of the ground”.
The main challenge, however, was the need for speed.
“We managed to spec and design the pipe in half a day. It was made for us over a weekend, and then we had contractors working almost 24 hours a day to lay it,” Sharon says.
“We had to get everything done in such a public way as well, in the middle of Parnell, with lots of media interest and pressure to minimise noise and disruption and keep traffic flowing and businesses open.
“It took 20 days until we had the temporary pump station working, and throughout the team pretty much worked 24/7, in shifts. There was real pressure on our operations engineers.”
At time of writing, rubble was still being removed, and a structural liner to support the sewer was being manufactured in Dubai. Created with climate change in mind, it is anticipated to last 100 years.
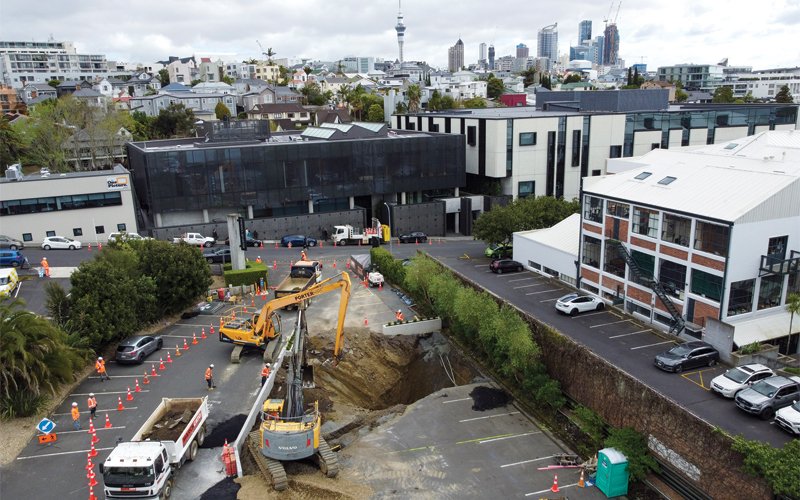
The 13-metre-deep sinkhole opened up in a car park on St Georges Bay Rd, Parnell, Auckland. Photo: Watercare
Lime kiln repairs
Jan Snyman FEngNZ IntPE(NZ) answered the phone at 6am on a Sunday. During the night, the main lime kiln at the Kinleith Mill in Tokoroa had overheated, causing its protective lining of 300-millimetre-thick refractory bricks to collapse and its carbon steel shell to corkscrew, so that it looked like a 78-metre-long Christmas cracker. But it could have been worse. “Had it rotated an hour longer, the whole thing would have melted and catastrophically collapsed,” says Jan, founder and Managing Director of Rotorua-based mechanical engineering consultancy Index Engineering. “I got the call saying ‘We have a little job for you’.”
That little job turned out to be the ultimate high-pressured emergency fix. Kinleith is Oji Fibre Solutions’ flagship pulp and paper operation, and the affected kiln supplies three-quarters of the mill’s lime needs. Limping along at 25 percent was potentially going to cost millions, so Index had no time to lose. By the end of Monday, the firm had called in two 250-tonne cranes to cradle the kiln and was busy designing a temporary structure capable of supporting 170 tonnes (within three days the slab had been poured and was starting to dry). Meantime, Jan had sketched out a replacement for the damaged shell section and engaged Wellington-based Acme Engineering to manufacture it. By the time Acme’s truck arrived on site on day seven, the kiln was supported and the damaged section had been cut out. Alignment was critical. “We couldn’t just weld it up. There were 32 sets of docking gear on both sides between the old to new shell, with lugs and wedges to be adjusted to align the shell. You had to tension each bolt, and that lines the kiln up to where it is supposed to be. While doing that, we had a surveyor with us, plus 3D scanners running the whole time to get the alignment correct,” Jan says, adding that Index was in constant contact with the kiln’s European manufacturers, who hadn’t been able to send their experts to New Zealand because of Covid-19 restrictions.
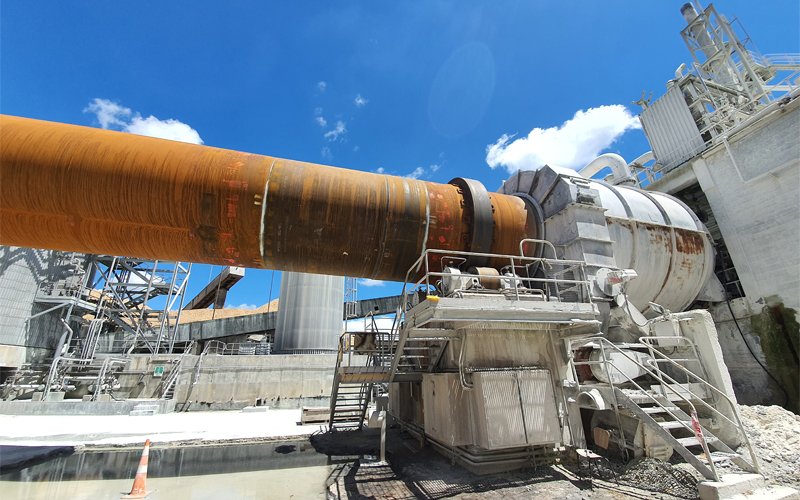
Completed repairs. Photo: Jan Snyman
Lining up the shell took a week. The welding, which involved one person operating from a scaffold above the slowly rotating kiln, took another 60 hours, with a crew of welders taking one-hour shifts. That was followed by replacing the broken refractory bricks, and then bedding in and testing. On the 22nd day after Jan received that early morning call, the kiln was run for the first time fully loaded, a remarkable feat given that overseas kiln specialists had predicted it would take months to fix. In September 2023, Index Engineering won a Gold Award from ACE New Zealand for the lime kiln repair project, with judges noting the “enormous pressure” involved.
Auckland Harbour Bridge repairs
When a freak 127-kilometre-per-hour gust of wind toppled a truck driving over the Auckland Harbour Bridge onto a load-carrying steel truss member in September 2020, the four central lanes were immediately closed. An initial analysis suggested it might take several weeks to return the bridge to safe operation, potentially costing the economy tens of millions. In the event, it took only 17 days.
Auckland System Management (ASM), which manages and maintains the Auckland state highway network on behalf of NZ Transport Agency Waka Kotahi (NZTA), engaged Beca to design the solution. There was no set programme.
“It was just a case of work as quickly as you can,” says Beca Technical Director of Structural Engineering Will Pank.
“The accident happened on a Friday morning. By Sunday, the team had done the assessment of the bridge structure and designed a temporary repair to get two more lanes, and that was fabricated on Monday and installed on Tuesday night. In the following two weeks the team completed the design, fabrication and installation of the repairs,” Will says.
The hard part, and the complex engineering aspect, was that when the member was broken all the internal tension force holding up the structure was released.
“The hard part, and the complex engineering aspect, was that when the member was broken all the internal tension force holding up the structure was released. We had to reinstate the dead-load forces into a replacement member by jacking the ends together to a specific force and were able to reset the bridge to its original geometry so that it could carry the full traffic load as it was before the break,” he explains.
“We used a bridge-specific live load which was measured from vehicle weights. That’s unique in New Zealand and rare for long-span bridges anywhere, but it meant that we could use a more realistic live load than the standards prescribe.”
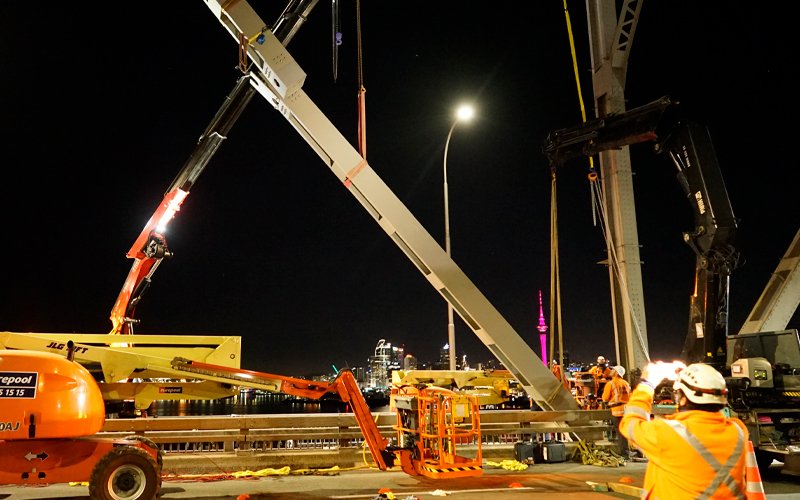
Lifting the new permanent beam into place. Photo: Will Pank
Crucial to success was close collaboration between all players, including the designers, constructors, NZTA and ASM.
“Our alliance contract meant we could bring all the right people to the table to work together from the beginning,” says Will, who adds that there was no margin for error, and no shortage of pressure.
Beca's work won an ACE New Zealand Silver Award.
The profession “really shone”
New Zealand’s geotechnical engineers must have cheered loudly on New Year’s Eve after a taxing 2023. “Frankly, our people are exhausted,” says Chair of the New Zealand Geotechnical Society Philip Robins FEngNZ IntPE(NZ) of a year that drew heavily on the profession’s resources.
The big challenge was Cyclone Gabrielle, when geotechnical engineers from all around the country raced to Hawke's Bay to help with everything from washed-out bridges to underslipped roads. There, and elsewhere, it was all about urgency, with the pressures of tight deadlines compounded by the remoteness of the work.
“It has been quite a strain on our profession,” says Philip, adding that the demands of 2023 highlighted the scarcity of geotechnical engineers in this country, exacerbated by the University of Canterbury dropping its Professional Master of Engineering Geology programme.
But 2023 did have a silver lining, giving the profession a bit of a nudge on climate change. “Rather than focus on design that is bulletproof, we need to focus on robust designs that are repairable,” he says, adding that “the profession really shone in terms of working together. We’ve been collaborative and creative.”
This article was first published in the March 2024 issue of EG magazine.