
8 Jun 2018
Queenstown-based CEO of Shotover Camera Systems, Brad Hurndell MEngNZ, won an Academy Award for the aerial camera he helped develop. He explains how engineering innovations have taken his team to the top.
When Brad Hurndell was a boy, he wanted to be a vet. But he knew from an early age that study didn’t hold great appeal for him.
“Once I got to school I didn’t think I had that five years of university in me,” he admits. When he left school he joined the Royal New Zealand Airforce as an aircraft engineer. But after three years, when the Strike Force he worked for was disbanded and he took voluntary redundancy, Brad was forced to rethink his views on study.
“I’d always enjoyed engineering and fixing things but I never actually envisaged I’d go to university. But it was a path that I had to come to because I couldn’t get to where I wanted to be without doing it.”
And it’s his engineering degree and subsequent experience that have helped him deliver what could be described as, literally, an Oscar®-winning performance.
Impressing the Academy
Brad, the CEO of Kiwi company Shotover Camera Systems, and three other design engineers won a 2018 Academy Award® for the concept, design, engineering and implementation of the Shotover K1 Camera System they developed. He received the award, in the Scientific and Engineering Award category, at a ceremony in Los Angeles in February.
“It’s great recognition for a Kiwi company that designs and makes its products in Queenstown,” Brad says.
The judging involved interviews and product demonstration, then judges researched the product, which included talking to owners, users and film producers.
Brad says he was extremely excited to hear of the win and proud of what the company had achieved.
It’s great recognition for a Kiwi company that designs and makes its products in Queenstown.
“The win was great recognition that reinforced that we’re the top aerial camera system in the world. It was a really good way to benchmark ourselves and know that what we thought we were achieving, the community that we work in also recognises.”
The win was also a chance to rub shoulders with Hollywood elite – Sir Patrick Stewart, of Star Trek fame, presented the award. “It was a fantastic experience. It was not too dissimilar from other awards but the level, the people in the room, were at the pinnacle of film technology.”
Camera action
The Shotover K1 camera is a six-axis, gyro stabilised, helicopter-mounted camera system manufactured in Queenstown. The camera’s carbon-fibre structure allows for a light, but strong and safe product. It’s used for shooting major movies and other productions such as television commercials.
“We get them all ready and then we test fly them and make sure everything’s perfect and then the customer comes to training, or we do training at their location.”
There are 18 Shotover K1 cameras in the world with just one based in New Zealand. They sell for around US$475,000 and customers rent out the cameras, or shoot the productions themselves.
When Brad and the other engineers started designing the Shotover K1 in 2009 there were already aerial cameras in use.
“They’ve progressed over the years from handheld cameras to different types of rigs and robotics.” Their goal was to improve on what was already out there.
“Many of the shareholders in the company are in that industry so they wanted to be pushing the boundaries.”
Key challenging design aspects were around stability and safety, as well as getting the right software, sensors and structure all working together as one unit.
“But then there’s also obviously the safety aspect and being on a helicopter, being lightweight, being able to transport it around the world. All of those aspects come together and start to fight each other so you need to get the right harmony.”
Developing a prototype took about 18 months and, from there, the K1 system was launched. Brad says the development was the fun part. “It’s the refinement and the testing, the improvements, that take the hard grind at the end. That last five percent is where it gets really difficult.”
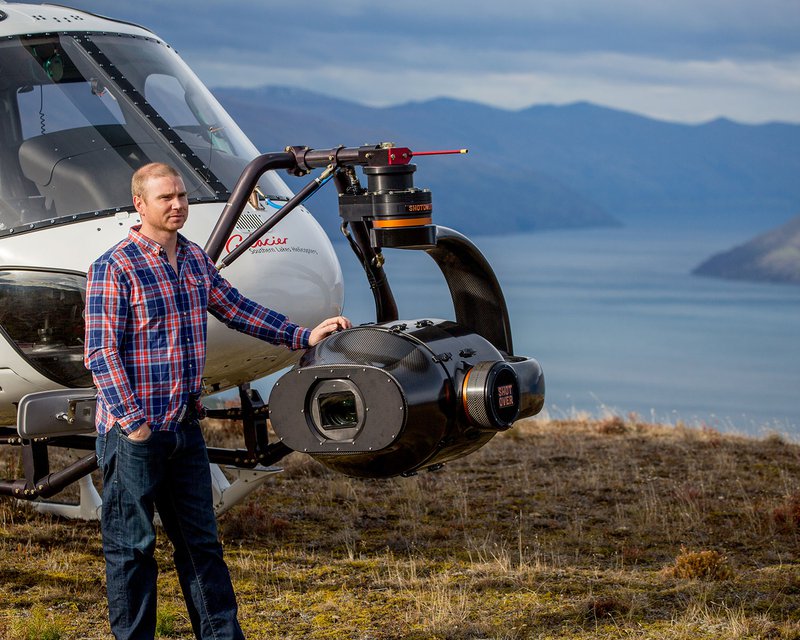
Brad Hurndell. Photo: Camilla Rutherford, camillarutherford.co.nz
He says the most challenging times in past years have been when the cameras have been used on movie sets in different time zones. In the event of a problem, the New Zealand-based team accesses the system remotely through an ethernet connection, at times working through the night.
So, what can it do that other cameras can’t?
“The freedom for the operator to be able to look anywhere and have full control, regardless of the aircraft’s movement is one of the key points. Also, the versatility of the number of cameras and lenses that can be incorporated, including two-, three- and six-camera arrays, so we’re fitting multiple cameras to the payload allowing super high-resolution VFX plates to be created.”
The camera can also shoot in 3D.
“We’ve had quite a few different combinations in different movies that have allowed shots to be performed that couldn’t be done before.”
Brad says each movie has its unique challenges.
“We had some 3D and dual lens combinations for The Hobbit, but then we also did six-camera arrays for Tarzan. We had some quite complex 3D work for Walking With Dinosaurs and also IMAX for Dunkirk. Each movie has its own twist – the directors are always trying something new so you never expect the same setup every time.”
View from the top
The camera first winged its way to Hollywood via a trade show and from there the team started promoting the product in earnest. But modest and measured, Brad reveals he never expected this level of success.
“You just put your head down and keep working and you keep trying to please your customers.” However, he does take time to appreciate the view from the top.
“There are definitely days when you’re in a helicopter and you’re looking out the window and you think ‘this is pretty amazing’ – especially down in Queenstown where the scenery’s awesome. But I’ve been lucky enough to fly in New York, Dubai, Los Angeles, Germany, Switzerland – a lot of places where a lot of people would be eager to go.”
In a chopper, his role is either end-of-line testing, operating the system at the R&D testing stage or giving demonstrations and training customers.
When you can tick “win an Academy Award®” off your bucket list, what’s your next business goal?
“For the K1 that’s probably as high as it gets. It would only be if we won another one for something else, a particular application – we have a few new products and new specific technology for a new movie coming up so that’s mixed in the opportunities.”
Meanwhile, Brad’s enjoying the win.
“I think it’s just another great example that New Zealand companies are able to see an opportunity and then put in world-leading engineering and innovation to the design and then have that recognised by the rest of the world.”
This story originally appeared in EG magazine. To subscribe to EG, email hello@engineeringnz.org