
1 Aug 2017
Holmes Consulting’s Hamish McKenzie and Joe White talk about the challenges of strengthening Wellington’s Majestic Centre during what’s been described as New Zealand’s most complex seismic project.
From the get-go, this was an undertaking of Herculean proportions: a five-year, $83.5 million multi-agency project to lift the seismic capacity of Wellington’s tallest building – the iconic 116-metre high, 30-storey, CBD-located Majestic Centre – from around 35 per cent New Building Standard (NBS), to 100 per cent NBS all while it remained fully tenanted.
It’s been described as the most complex seismic project ever undertaken in the country. Holmes Consulting’s Wellington-based Business Manager, structural engineer Hamish McKenzie MIPENZ, explains: “From analysis to design solutions to implementation, this was a grunty, multi-faceted and technically challenging project. As structural engineering consultants, we were applying structural engineering solutions on a scale and with a level of complexity that hadn’t been seen in New Zealand before, alongside developing cutting-edge techniques that will inform future seismic design here and around the world.”
Then-Wellington-based Project Director, Joe White MIPENZ –now head of Holmes’ Netherlands office – agrees. “The logistics of applying engineering solutions to a building that was in service – there were 2,700 people in it every day – meant this wasn’t a normal project where completed designs are cross checked, cross referenced and then delivered to the contractor,” he says. “By necessity, it was a staggered design and construction approach: as soon as a single design was completed it was passed to the contractor to begin work."
In effect, we were working on two fronts, working with the contractor on site, reviewing their work and resolving issues, while still developing new designs for other parts of the building back in the office. This was challenge with a capital ‘C’.
Critical structural weaknesses
In late 2011, on the back of the Canterbury earthquakes, Holmes was seismically assessing a number of Wellington properties for its client, Kiwi Property – the Majestic Centre among them. Holmes’ initial qualitative assessment of the building had thrown up a few question marks and Kiwi Property asked for more detail. The engineers embarked on a series of quantitative seismic assessments of the building, which crystallised some of the deficiencies question-marked in that earlier review. “In particular, we uncovered three critical structural weaknesses,” says Hamish. “Insufficient flexural and shear strength of the level five transfer beams; limited confinement, and insufficient flexural and shear strength of the two central C-shaped shear cores; and insufficient bearing area, reinforcement, and flexural and shear strength of the core foundations.”
In the case of the transfer beams, the load from every second column above the beam is transferred out mid-span to the columns on either side, the ones that continued down through the building. Hamish says “Our analysis showed that while at certain loads it was possible to have failure of that transfer beam and still have capacity to be above the earthquake-prone building threshold of 33 per cent NBS, failure at higher load levels would mean losing effectiveness of the perimeter frame above the beam, and facing potential critical failure of the building.”
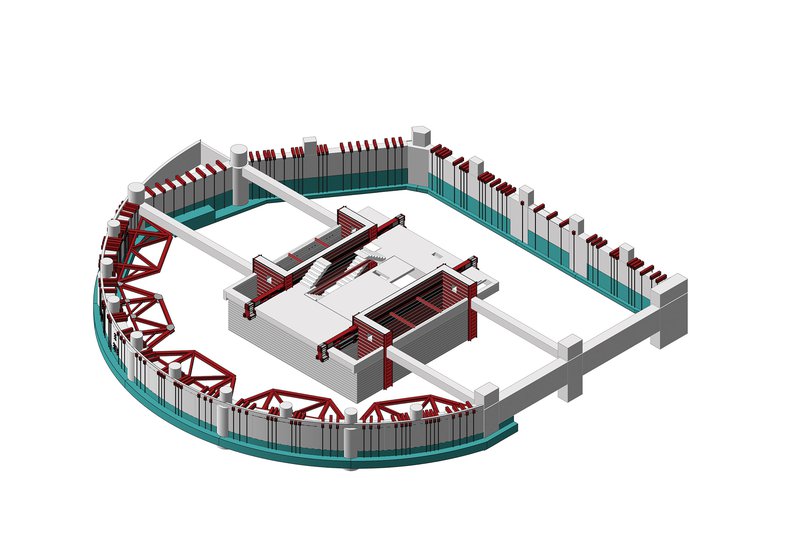
Isometric view of Level 5 transfer beams after strengthening. Grey = existing beam, green = new beam. Image courtesy Holmes Consulting.
Mitigation involved strengthening the existing beams by casting a deeper reinforced concrete transfer beam underneath the original ones and clamping the layers together with steel pre-stressing elements – the strength of both new and existing elements now combined.
So far, so good, but one of the big issues the team had to overcome was how to anchor the new transfer beam reinforcing effectively into the existing columns when those columns were already packed to the gunnels with their own reinforcing. Hamish says “Normally you’d pass beam reinforcing bars through the column and use an internal beam-column joint but we couldn’t do that here. So, our design solution involved passing bars either side of a column and effectively clamping them on to its back side.”
Meanwhile, the team was also tackling the shear core confinement and strengthening issues. The C-shaped shear cores can be likened to the central spine of a building. While their function is primarily structural, they also act as a conduit for service infrastructure – think lift shafts and associated machinery and rails, and service risers – not to mention adjacent bathrooms and an egress stairwell.
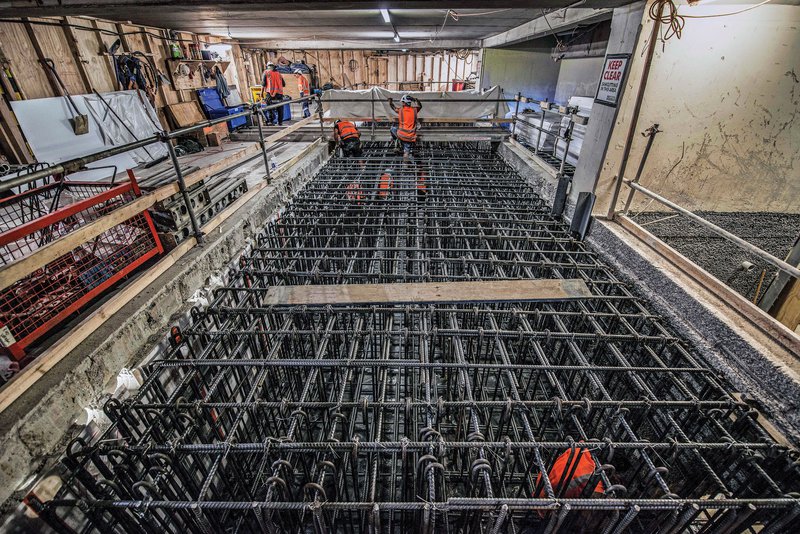
Preparing for mass concrete pour to new foundations. Photo courtesy Grant Sheehan.
“The Majestic Centre’s two shear cores were very lightly reinforced and consequently prone to exploding under heavy cyclic load. It’s exactly what we saw in Christchurch; significant shear wall failures due to lack of confinement and low reinforcing ratios,” says Hamish.
Holmes’ ingenious solution involved wrapping each shear core in a metal jacket. Steel angle sections were welded together to create 131-metre vertical lengths of steel running up each corner of each core; horizontal steel plates, or bands, run across the faces of each core wall surface (looking much like rungs on a ladder); and each of those bands (or rungs) is clamped through the wall to a similar band on the other side using bolts.
And the effect of all this additional metal? Hamish explains: “In a big shake, the greater tension reinforcing of the angle sections on the corners increases the flexural capacity of the wall; the additional confinement reinforcing provided by the bands and through-bolts prevents concrete from crushing and exploding outwards; and the horizontal bands (or rungs), in addition to providing confinement, markedly increase the shear capacity of the walls.”
Then there were the shear core foundations to think about. “Both foundations were independent of each other and sitting on a sloped site with variable ground conditions,” says Hamish.
The west foundation was higher than the east foundation, which sat over a steeply inclined bank. We had real concerns about rotational failure. Plus, neither of the foundations were big enough and were too lightly reinforced.
Holmes’ solution involved overlaying the existing foundations with a single reinforced concrete mat foundation complete with post tensioning reinforcement, and adding a run of vertical piles into the soft soil under the new foundation’s western edge. “The result was an increased bearing area, reduced settlements and significant gains in ground stabilisation,” says Hamish. And all this – what was in places a two-storey-high solid reinforced concrete block – constructed at the bottom of a basement car park, five-storeys below the street entrance.
Monumental challenges
So, what about those logistical challenges? Joe says “Accessing the various worksites presented monumental challenges to the team.” Take the shear core foundation, for example: the car park ramps and floors were designed for passenger vehicle use, not heavy trucks or machinery. But 1,500 cubic metres of excavated soil were removed by pick-up trucks and utes, up and down the ramps. The piling rig was stripped down to the smallest nuts and bolts and transported on the back of those same vehicles and rebuilt in the basement. Reinforcing materials were shifted in the same manner. And just imagine a line of concrete trucks up and down Boulcott Street as far as the eye can see, pumping 1,000 cubic metres of concrete from ground level through a length of hose winding through the car park to the basement. Astonishingly, bar the day of the big pour, the car park remained operational.
“One of the worst problems was accessing the shear cores,” says Joe. “Not only are they located in the centre of the building, they function as lift shafts, are covered in data cabling arrays for the whole building, house the fire dry riser and are surrounded by building services, such as the main fresh air supply for the building’s air conditioning system. Adjacent to one core is the building’s main stairwell and by the other, are each floor’s bathrooms and associated plumbing. You’d struggle to make it harder or more expensive to actually get to those walls, let alone place steel strengthening on them. It really was very, very challenging.”
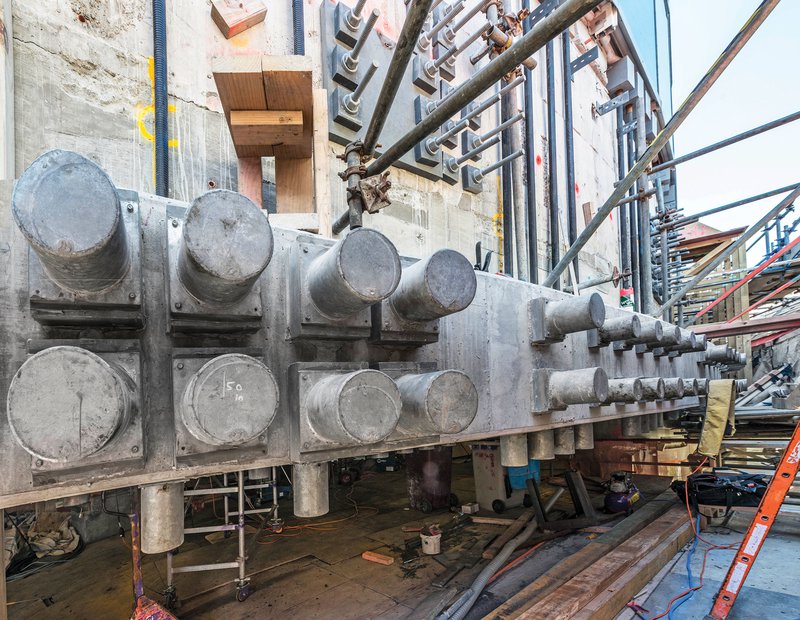
Transfer Beam with capped pot tensioned bolting. Photo courtesy Grant Sheehan.
As for accessing the level five transfer beam: “Around the curved southern half of the building, the beam sits outside the building envelope, 12 metres above people’s heads as they walk in at street level, requiring a working platform at that height, meaning that anything we designed had to be able to be transported onto it,” says Joe. Heading south east around the building, the beam then passes back inside the building and directly over the main escalators – think working platform location again. Carrying on to the north, it passes through a gym, continues over a swimming pool, through two plant rooms holding the main transformers for the building and extends over the top of the car park entrance, which, for obvious reasons, could not be blocked. “This was no temporary structure,” says Joe. “This was something the construction guys worked off every day for a year or two. It was a serious piece of engineering design in its own right.” Little wonder then that at its peak, this project demanded the full-time attention of 15 structural engineers across three Holmes offices.
The 7.8 magnitude Kaikoura earthquake struck just after midnight on 14 November 2016, just as this project was into its concluding stages. It was both a test the building passed with flying colours – it suffered only minor damage, none of it structural – and a timely reminder of the essential life safety benefits of this Herculean undertaking. But beyond that critical outcome the project appears to have achieved so much more, proving strengthening of existing significant structures can be realised despite severe physical, functional and financial constraints.
Its success celebrates not just the exceptional engineering design, the investment vision of the building owner, the determination and perseverance of its contractors, and the endurance of its tenants (and neighbours), but also the clear environmental benefits delivered in the preservation of existing resources. Indeed, for this hero project, the real celebration is that its success will endure well into the future.