
13 Jun 2024
How can Industry 4.0 technologies help Aotearoa’s manufacturers to work smarter, not harder, and is there a flow-on benefit for the way people view engineers?
From making chocolate chips to computer chips, Aotearoa’s diverse manufacturing sector contributes $23.28b to our gross domestic product. It directly employs 222,400 people and accounts for more than 60 percent of the country’s total export value, according to the Technology Investment Network’s (TIN) New Zealand Advanced Manufacturing Report 2023. The sector includes household names like Fisher & Paykel Healthcare, large firms such as precision manufacturer Buckley Systems, Red Stag Timber and smaller operations such as iwi-owned milk processing company Miraka and sustainable knitwear brand Untouched World.
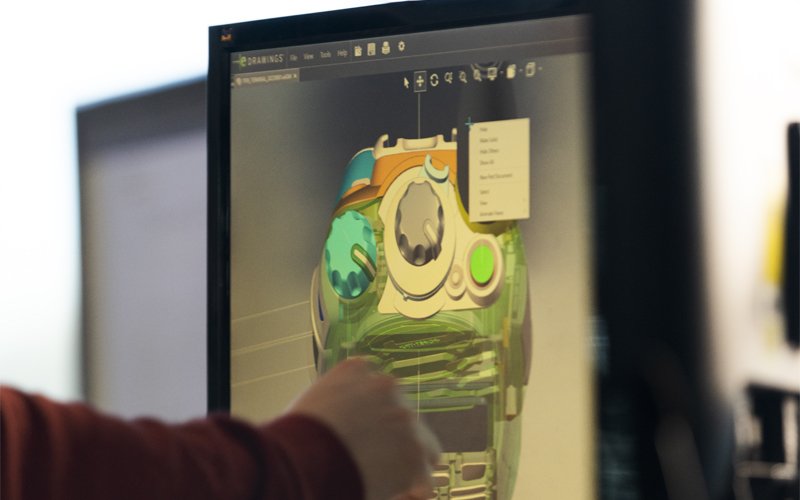
New Zealand's manufacturing industry accounts for more than 60 percent of the country’s total export value. Photo: New Zealand Story
The country’s top-earning manufacturers are “working smarter not harder” by deploying Industry 4.0 technologies, the TIN report notes. Industry 4.0 – or the fourth industrial revolution – involves greater automation, with smart technologies (for example robotics, digital twins and artificial intelligence [AI]) and data combining to monitor and control processes in real time. As well as increasing productivity by as much as 30 percent, advanced technologies can help overcome geographical disadvantages, boost profitability, enhance competitiveness, reduce carbon emissions and help to generate higher-value jobs by automating lower-level tasks.
There’s still a perception in New Zealand that manufacturing is a dirty, basic industry and it’s all men.
But industry observers warn New Zealand is 10 years behind Europe in adopting these technologies. The now-defunct Productivity Commission found local companies are working harder than many overseas rivals, yet creating less value.
Industry undergoing “a fundamental shift”
Those who fail to embrace smart processes and products will get left behind, says Advanced Manufacturing Aotearoa (AMA) Chief Executive Catherine Lye.
“It is a concern. Industry is undergoing a fundamental shift with the application of these advanced technologies, but New Zealand manufacturers are a laggard.”
Catherine says the key is to support manufacturers by raising awareness and understanding of these technologies and then accelerating investment and adoption.
She admits significant investment is required while it can also be “… overwhelming, particularly for smaller firms, to wrap their heads around all the different options”. Catherine says the AMA will play a key role in strengthening the country’s manufacturing network. The aim is to support the adoption of smart, modern technologies and processes that enable a more productive, sustainable and globally competitive sector.
“...we need to make engineering sexy again”
Meanwhile, the Minister for Small Business and Manufacturing, Andrew Bayly, has set up a Manufacturing Productivity Advisory Group (MPAG) comprising industry people and strategic thinkers to look at funding opportunities. A key priority is addressing the way the industry is viewed.
MPAG is chaired by United Machinists Chief Executive Sarah Ramsay, who says it has become rapidly apparent that manufacturing “is not a sector in itself but a function that underpins all of New Zealand’s major export sectors”.
“There’s still a perception in New Zealand that manufacturing is a dirty, basic industry and it’s all men. We don’t associate it with making rockets or pharmaceuticals or healthcare – all industries where there’s so much innovation and opportunity.”
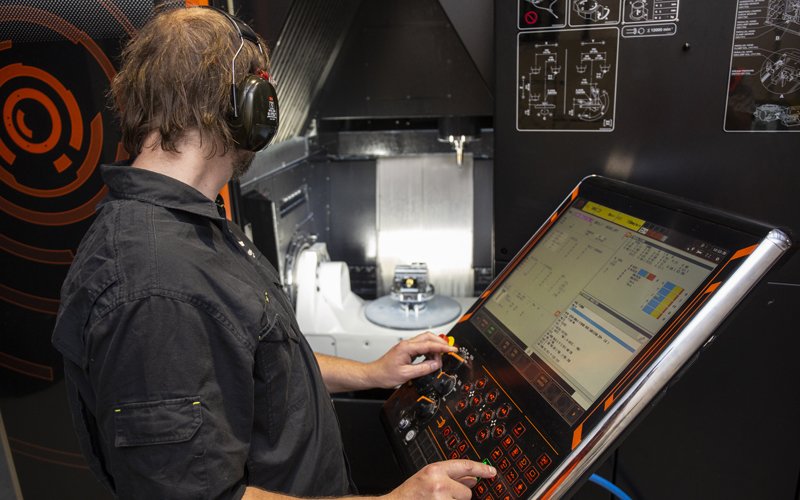
CNC Machinist Matt Topping proves out a component on the Mazak VARIAXIS fully automated machining centre. Photo: United Machinists/Graham Warman
She says the out-of-date stereotype affects how the sector is seen by students and schools, as well as investors.
“We need to directly address this: we need to make engineering sexy again.”
Sarah says this doesn’t need to be costly, citing Engineering New Zealand’s Wonder Project, the schools programme which aims to inspire rangatahi with science, technology, engineering and maths, as an example of a “fantastic” initiative.
She adds that micro-credentials, obtained via short-burst training, offer qualifications in new technology that can help the existing workforce upskill.
A “learning factory” for students and industry
Professor of Smart Manufacturing Dr Xun Xu FEngNZ is the only non-industry person invited to be part of MPAG.
In 2016 Xun, hailed as one of the world’s most influential professors in smart manufacturing by Smart Manufacturing magazine, set up Aotearoa’s first and only Industry 4.0 laboratory at the University of Auckland’s Department of Mechanical and Mechatronics Engineering.
He wanted to create a “learning factory” for both future engineers (students and postgraduates) and industry. Unlike most research labs, Laboratory for Industry 4.0 Smart Manufacturing Systems (LISMS) is like a miniaturised factory. Conveyor systems and machine tools whir away as robots direct parts.
“It provides a unique setup to learn about advanced manufacturing technologies, and it also serves as a ‘testbed’ for companies to come and try out different industry 4.0 technological solutions in an environment that is akin to their own.”
When one job is automated, another job is often created. It may not be in a similar area, so factories need good re-skilling programmes.
Up to 30 companies annually visit the lab, which often results in collaborative projects. LISMS’s clients include ABB, Air New Zealand, Ports of Auckland and Fletcher Steel.
An example of such an industry-based project is developing an inspection system for ABB in Napier, which wanted to automate its inspection processes of an uninterruptable power supply (UPS) chassis to avoid errors and repeats. The students developed a bespoke, low-cost, easy-to-operate solution – and trained staff – after an earlier foray into robotics proved too expensive.
Xun says robots are good, as long as companies can afford them, train their staff and use them to their full potential. But many New Zealand businesses are “small to micro-sized” with very low capital intensity. A low-cost digital solution is often more fit for purpose.
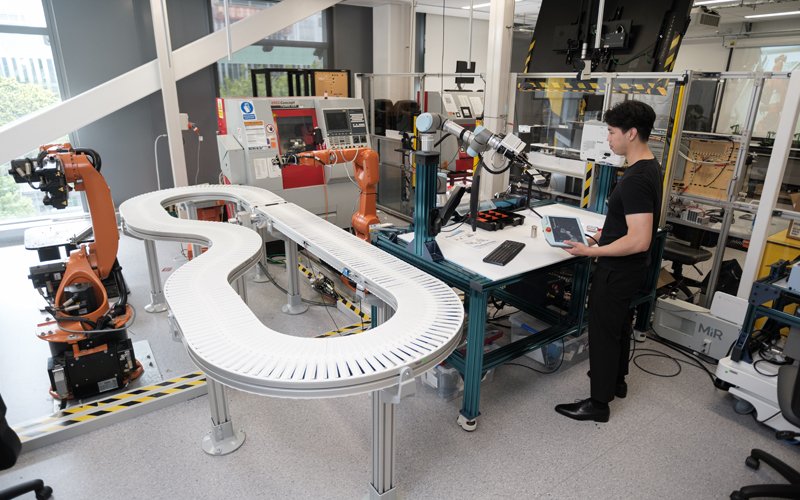
The “learning factory” inside the Laboratory for Industry 4.0 Smart Manufacturing Systems. Photo: ©University of Auckland
LISMS is also looking into how technologies can be developed for sustainable manufacturing, particularly considering workers’ welfare. For example, human-centric automation is demonstrated by operators working with, and supported by, collaborative robots, or co-bots.
Xun says humans are still needed for some more complex and highly dexterous tasks.
Automation could mean that fewer people would be needed to perform some repetitive jobs in a factory, but businesses need to look after their workers.
“When one job is automated, another job is often created. It may not be in a similar area, so factories need good re-skilling programmes.”
Creating the “Machine shop of the Future”
Sarah and Alex Ramsay are second-generation owner-operators who bought their Dunedin-based precision machining company United Machinists from Alex’s parents in 2016, with the aim of creating the “Machine shop of the Future”.
It’s a thriving example of why companies need to combine engineering skill with strategic leadership.
Sarah says Chief Technical Officer Alex is an “incredible tradesperson” who started helping in the workshop as a four-year-old.
Meanwhile, Chief Executive Sarah brings the commercial nous as a former business consultant who previously owned a marketing agency.
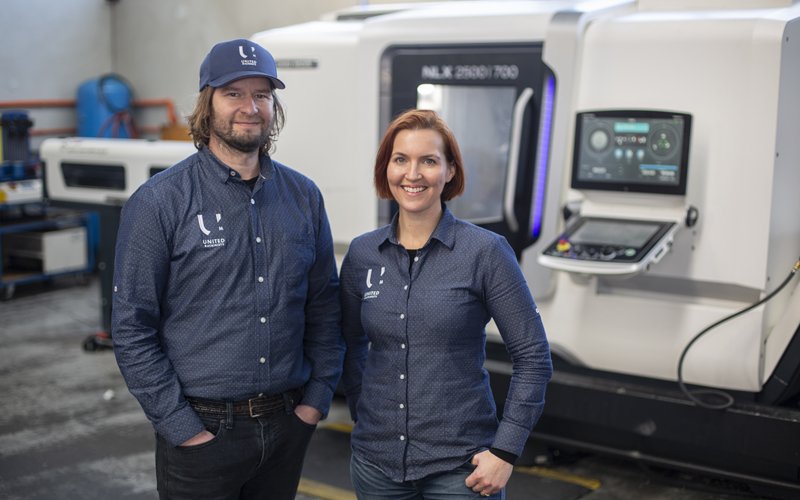
Alex and Sarah Ramsay, owner-operators of United Machinists. Photo: Supplied
A self-described “high school drop-out with no formal education”, Sarah is now an award-winning business leader who holds numerous governance positions and writes a fortnightly column for the Otago Daily Times. But, she says, her most unusual achievement is applying things that are common practice in other sectors to manufacturing.
In 2018, she set about establishing the company’s brand. A year later the firm started on its Industry 4.0 journey by moving to a fully automated, digital scheduling system using Enterprise Resource Planning software.
Having better control of data and greater visibility of workflow has boosting earnings substantially.
“In the first month we realised we were losing money on 45 percent of our jobs, and now it’s about three percent.
“We were under-estimating. Engineers constantly undervalue how brilliant they are.”
The money saved helped fund a new workshop in 2020, with a lights out 24/7 manufacturing facility, whereby robot and automation systems operate on their own.
It also allows the company to keep investing to grow their precision machine capabilities, automating wherever possible. United Machinists has started to move into processes like 3D printing, engraving and anodising. Clients include Shotover, which designs high-performance camera systems used on the likes of the X-Men movies. Automation has opened it up to new sectors such as aerospace, defence and medical technology.
Sarah says the team is “no longer suspicious about AI taking their jobs, but excited” AI will do the bulk of the “grunt” quoting and programming work while they upskill and move into more challenging roles.
United Machinists has grown “significantly” on the back of its investment in Industry 4.0: it has increased staff by 50 percent, while more than doubling revenue and profitability.
“That’s a pretty good metric. We never could have done that without automation.”
Nor, she adds, do staff need to work overtime.
“What I see go wrong in industry so often is that these programmes and implementations aren’t being done to bring everybody along for the ride.”
Starting “... before Industry 4.0 was a term”
Tauranga’s RAM3D (Rapid Advanced Manufacturing 3D), a large provider of additive manufacturing, was a pioneering Australasian firm when it began developing metal 3D printing in 2009.
“It was exceptionally early days. We started well before Industry 4.0 was a term,” says Director Warwick Downing.
Additive manufacturing offers a more agile and efficient way to produce complex metal parts that are lighter and stronger, and cost less.
The next few years were “a big learning curve” for both the start-up and prospective customers.
“After a number of years building our knowledge and a customer base, we started RAM3D in 2013 to take the technology to market.”
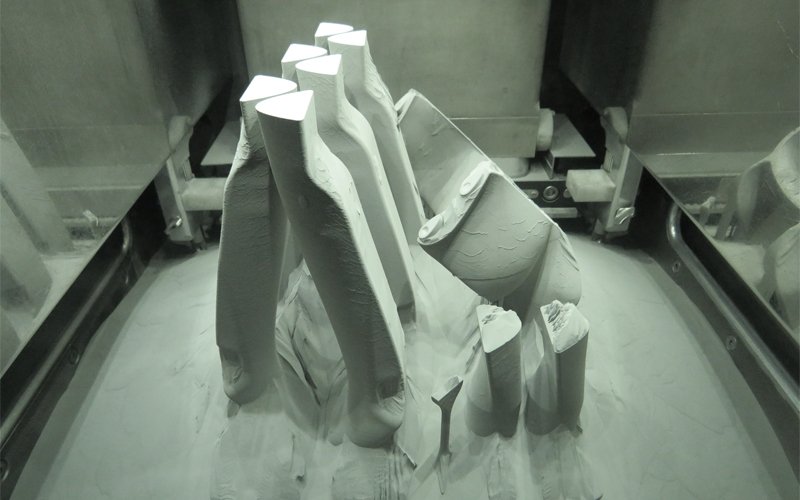
Titanium handlebar extensions being removed from the machine after laser powder bed fusion printing. Photo RAM3d
More than a decade later, RAM3D has 11 staff and 13 machines. Around 80 percent of its work is offshore. It includes projects in aerospace, cycling and defence. Some 8,000 RAM3D-manufactured components have been launched into space, including a current project which put sensors on the moon. Meanwhile, its bespoke handlebar extensions are used by many Tour de France cyclists as well as the New Zealand track-cycling team.
Design and analysis are key to creating leading-edge components. Humans still need to have an input “to maximise effectiveness” in manufacturing, says Warwick.
“New technologies are enabling new performance standards, but if you don’t understand what you’re trying to achieve, you won’t get there.”
This article was first published in the June 2024 issue of EG magazine.