
4 Dec 2019
It’s a space rover like no other – essentially a ball that moves by jiggling itself around, and NASA hopes to use it to some day explore other planets. New Zealander Hammond Pearce was lucky enough to be handed the controls.
As part of a National Aeronautics and Space Administration (NASA) internship, Kiwi Hammond Pearce helped design a prototype robot’s control systems earlier this year. One of four students selected for a New Zealand Space Scholarship, he spent 10 weeks working and staying at NASA's Ames Research Center in California with 250 other interns from around the world.
The computer systems engineering PhD student at the University of Auckland was assigned to the team developing “SUPERball”.
“It’s a very unique design, not your normal space rover with wheels,” he says.
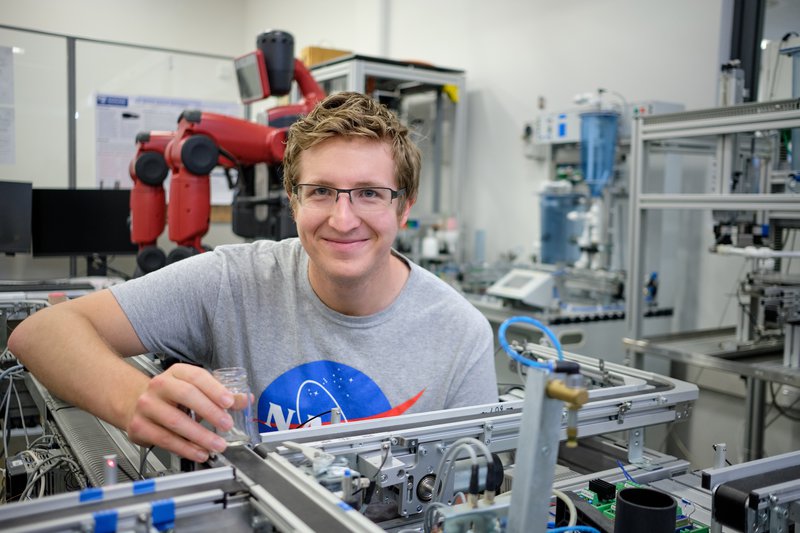
Hammond Pearce
The work the interns were involved in was as wide as what the research facility does – everything from developing wings for commercial aircraft, to testing biomarkers for detecting life on other planets.
“While some interns didn’t know what team they’d be in before getting there, I was fortunate in that I did know who I’d be working with. Before I arrived, I read all the papers the research group I’d be working with at NASA had published so I could hit the ground running.
“My role was to do a proof-of-concept for a new software control of the explorer. The robot is very strange. Because it’s not your typical wheel design, controlling it is very difficult. NASA has worked on a number of algorithms for it that kind of work and kind of don’t.”
SUPERball is a two-metre tall, collapsible robot based on a tensegrity design, made up of cables and rods. Its flexible structure allows it to withstand substantial impacts and move around on challenging ground.
“What my supervisor wanted me to do was create a new, machine-learned model that could drive it. So, we made an open-loop controller based on a spiking neural network, and then I tuned it on my computer to make it work under simulation.”
It’s a very unique design, not your normal space rover with wheels.
Once the team was satisfied with the computer simulation, they applied it to the real thing at Roverscape, an 11,500-square-metre outdoor facility where NASA tests planetary explorers on a gravelly, Martian-like surface.
Happily, the robot performed well, rolling across the ground without too much difficulty.
Hammond was particularly impressed by what he saw at NASA Ames.
“It seemed like there were a lot of moving parts on the base, and I really enjoyed it. Everyone was really friendly. It seemed like, from an outsider’s point of view, the sort of place where people who work there really want to be there.”
NASA Ames is a huge research centre in the heart of Silicon Valley. Hammond’s time there coincided with the anniversaries of the Apollo Moon landing and the research facility’s founding in 1939, both of which were marked with a series of celebrations.
He says while the technology on site is in varying states of modernity, a lot of it is still in working order and repurposed for new projects.
“They’re updating and are still using a lot of the very old equipment – including from the 1960s, such as the vertical motion simulator, which was originally used to train Apollo astronauts. Then they updated it and it was used to train Shuttle pilots. Then they updated it again and it’s now used to train Orion and Dragon pilots.”
It’s the same machine with new technology inside it, he says.
“They’ve also got an Arc jet, which they use to simulate re-entry vehicles going all the way back to Mercury, and they’re still using it. But if you’ve got something that fires a huge amount of plasma at something bolted to a stick, you don’t really need to change that.”
Once he completes his PhD, Hammond wants to get into post-doctoral research with an eye on a professorship – potentially at universities in the United States. While he won’t necessarily be pursuing space or robotics-related fields, he knows his time on SUPERball was worth it.
“Once you’re on an academic pathway, the research you do is always the sum of everything you’ve learnt up to that point.”
He says for any project involving safety-critical control systems in the future, he has an amazing case study to refer to.
“The machine-learning and the spiking neural network I worked on – those apply to a huge number of scenarios, not just controlling a robot. Using those tools, I can take what I learnt and apply it to any number of case studies or research.”
This article was originally published in the December 2019 issue of EG magazine.