
16 Dec 2024
Aquaculture – the farming of aquatic plants or animals – is said to hold significant economic promise for Aotearoa. Here are some of the ways engineers are involved in projects aimed at boosting the sector’s profitability and sustainability.
Putting eyes underwater. That’s how University of Canterbury Engineering PhD student Tim Rensen describes the programme he’s leading to develop an AI-powered underwater drone capable of automatically scanning mussel farms. It’s a project fraught with difficulties, including a highly dynamic and often hostile operating environment, plus water pressure that is “constantly trying to fill the electronics tube with salt water”. But if New Zealand is going to meet the government-set target of tripling aquaculture exports by 2035 while also ensuring sustainability, these are the kind of challenges that engineers and others are going to have to find answers to.
Tim heads a team of 10 at Christchurch-based startup ŪWAI Robotics that includes electrical, mechatronic and software engineers. Using advanced simulation and edge-AI computing technology, their smart, self-navigating drone is capable of helping mussel farmers to measure mussels – useful for determining harvest times – and predict yields. Even in this initial limited application, the benefits of automation are significant, Tim says.
New farming, monitoring and harvesting methods need rapid and frequent feedback to increase the rate of innovation in aquaculture and fisheries.
“Currently, underwater monitoring must be done by divers, dredges or by hauling heavy and delicate structures out of the water for inspection. Underwater remotely operated vehicles are becoming more common, but they still require an intensely focused pilot and produce terrabytes of visually stunning but useless raw data images. It all makes underwater information expensive, dangerous and not scalable.”
The ŪWAI smart drone, by contrast, eliminates the issue of pilot fatigue, making it a far more scalable solution. As for the data collection and analysis side, Tim points out that ŪWAI originated from a computer vision research group, UCVision, led by Professor Richard Green.
“So, our strength is the automated 3D image analysis to distil critical insights from vast amounts of raw data using both edge and cloud processing,” Tim says, adding that in addition to mussel farms, the drones could potentially be deployed on seaweed and scallop farms, fish cages, and marine infrastructure, to name just a few applications.
If ŪWAI can successfully commercialise its work, it should help to de-risk aquaculture by introducing far more accurate and effective monitoring for things like invasive species.
“New farming, monitoring and harvesting methods need rapid and frequent feedback to increase the rate of innovation in aquaculture and fisheries,” says Tim.
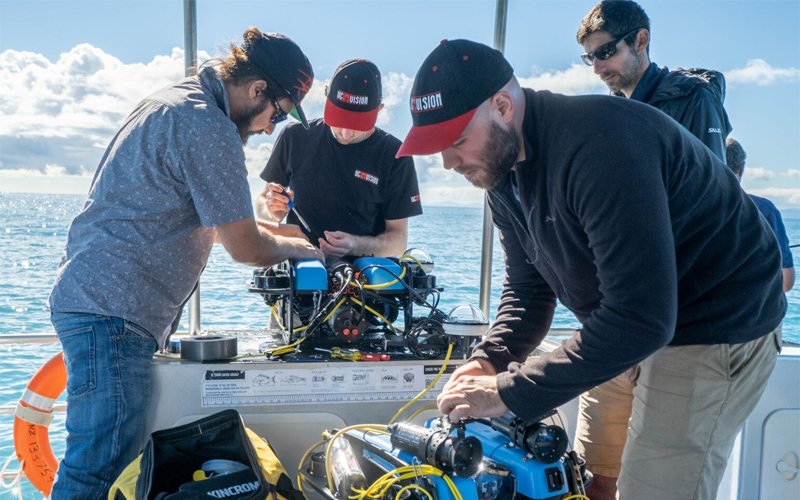
The ŪWAI Robotics team reconfigure underwater robots while testing new features at mussel farms in Tasman Bay. Photo: University of Canterbury
“This will allow aquaculture farmers, offshore energy producers, iwi and regulators to make the best possible decisions in the face of rapid climate change, enhancing food security, environmental responsibility and sustainability.”
That last point is important. If made economically viable, mussels and other aquaculture products have the potential to replace higher-carbon-footprint protein sources. What’s more, underwater robotics can help to protect our oceans and coastline, according to Tim.
“We strive to make ŪWAI robotics a global company with our core value being enhanced environmental and social sustainability.”
Creating “the fish processing factory of the future”
There is plenty of other work happening around the motu involving the application of smart engineering to aquaculture and fisheries. Among the most ambitious is the Plant & Food Research-led “Cyber-Marine” project, funded by the Ministry of Business, Innovation and Employment's Endeavour Fund, which is attempting to use AI to create the fish processing factory of the future.
Project leader Dr Susan Marshall says Cyber-Marine begins from the standpoint that we need to think about seafood in a whole new way. Currently, a fish such as hoki is processed for its meat, with the rest discarded or turned into low-value products.
“But around 50 to 60 percent of a fish is not fillet. Based on the biomass, we should be able to make more money out of the non-fillet part, particularly because that’s the material that has all the interesting bioactive molecules, with lots of protein, Omega 3 lipids – all kinds of interesting things. It has massive potential, but most of it goes to make fish oil and fish meal that’s worth about $2 a kilogram.”
Unfortunately, our traditional processing plants are blunt tools, while the material going into them is enormously complex and varied. Aotearoa has more than 100 commercial fish species, plus there are seasonal changes in composition to deal with. That all presents a huge challenge if your goal is to make full use of the seafood biomass and deliver maximum value. You can analyse the material’s composition chemically, but the results will only roll in long after the harvest has been processed.
The Cyber-Marine vision is that a seafood factory becomes a marine products factory, with AI tools used to calculate the most valuable combination of products based on composition and market knowledge. The biomass would be processed sustainably and efficiently, with extraction carefully sequenced to optimise the raw material, and with nothing wasted.
At this stage, the programme is into the fourth of five years, with researchers focused on compositional analysis of three exemplar species – hoki, mackerel and Greenshell™ mussels. A team at Victoria University of Wellington tackles the AI part, which involves converting an enormous flood of data into actionable insights.
“It is extremely challenging,” concedes Dr Owen Catchpole FEngNZ, Team Leader and Chief Engineer in the Food Processing Team within the Biotechnologies research group at Callaghan Innovation, a partner in the Cyber-Marine programme.
“You have to take the online measurements for marine material going into the factory and tell the factory, which has a suite of processing operations, in what order and how to do the operations to achieve maximum value or volume – both if possible. In future years, the AI might even be able to predict what the market is going to desire, although that’s in the realm of science fiction at the moment.”
Owen, whose background is in chemical engineering, uses the example of Greenshell™ mussels, which are low in oil content but high in phospholipids, prized for their neutraceutical applications.
The AI challenge there is to sequence the processing steps, he says.
“You could start with fat extraction, which might require the mussels to be completely dried. After that, you might process to recover proteins and other valuable things. Or you could start by extracting proteins and reduce the biomass until you’re at a point to extract the lipids.
“There might be a market shift, where lipids go down in value and proteins go up, so you could swap around the order of processing operations. The technical challenge is that each processing step exposes the remaining raw material to degradation and yield losses.”
If it works, there’s an obvious economic payoff – higher value exports, maximised revenue. But there’s also a sustainability benefit, says Owen.
“It will ensure full resource utilisation, and far more efficient use of energy and water both on-boat and in processing factories.”
Engineers have key roles to play in the project, from the AI, to plant design, process parameters and designing how material is processed in order to extract maximum value and yield.
“It’s about new technology development and building new factories, fitting things together, monitoring efficiency, water usage, electricity and all those good things,” says Susan, who hopes to have proof-of-concept sorted by the end of October, with prototyping to follow.
“This coming year is when the rubber meets the road.”
Testing in a controlled environment
With sheltered waterways at a premium, and increasing resistance to inshore fish farms, the next frontier of aquaculture production will be the open ocean. Still, it’s a punishing environment, and warming sea temperatures only add to the risk. One solution is to build mobile farms, capable of being towed to new locations when storms or temperature variation and conditions threaten, or to optimise seasonal fish growth.
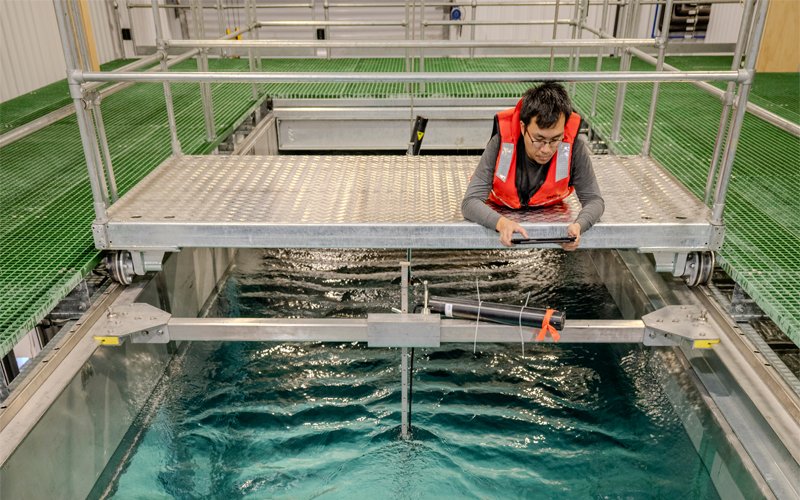
Plant & Food Research engineer Si Thu Paing sets up an experiment in the new 190,000L fresh water flume tank, designed to test performance of prototypes in an aquatic environment. Photo: © Plant & Food Research/Wara Bullôt
In Nelson, Plant & Food recently unveiled the country’s largest flume tank, which will allow scientists and others to road-test technologies for open ocean aquaculture in a controlled environment. Sixteen metres long and containing 190,000 litres of water moving in a recirculating uniform flow of up to 1.5 metres per second, it has a couple of critical advantages over in situ testing: it’s cheaper and far less risky.
Kevin Patterson, Plant & Food’s Head Engineer on the tank, says it was initially used as part of a precision seafood harvesting project, testing the towing performance of scaled-down models of trawl nets that have been designed to minimise crush and waste. Now the focus is very much on open ocean aquaculture.
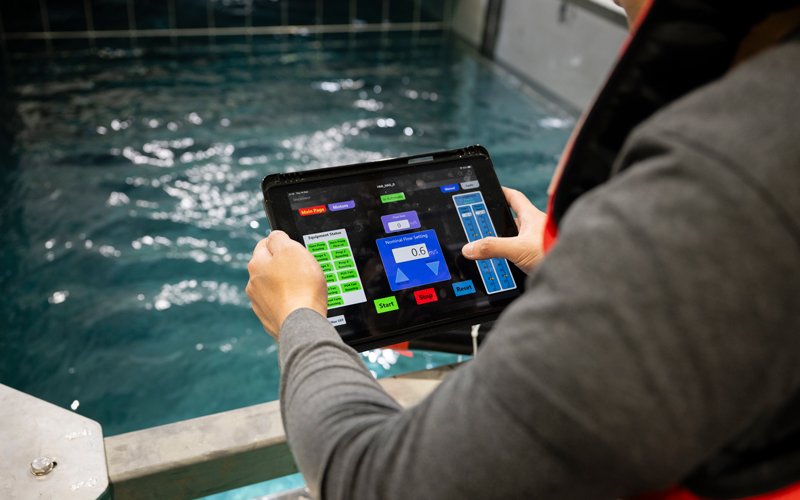
The flume tank can be programmed to generate uniform water flow conditions of up to 1.5m/s. Photo: © Plant & Food Research/Wara Bullôt
Engineering has been central to the flume tank project right from the conceptual design, which involved a lot of computational fluid dynamics modelling to achieve uniform flow, and the construction, which was handled in Christchurch. The biggest challenge so far has been cavitation from the propellors and problems with the propellor ducting.
“The cavitation was so bad that the vibration cracked the ducting welds,” he says, adding that the eventual solution would likely be a new propeller and driveshaft design that will eliminate cavitation.
This article was first published in the December 2024 issue of EG magazine.